Get the latest news from tracezilla
4 ways to succesfull stock-taking
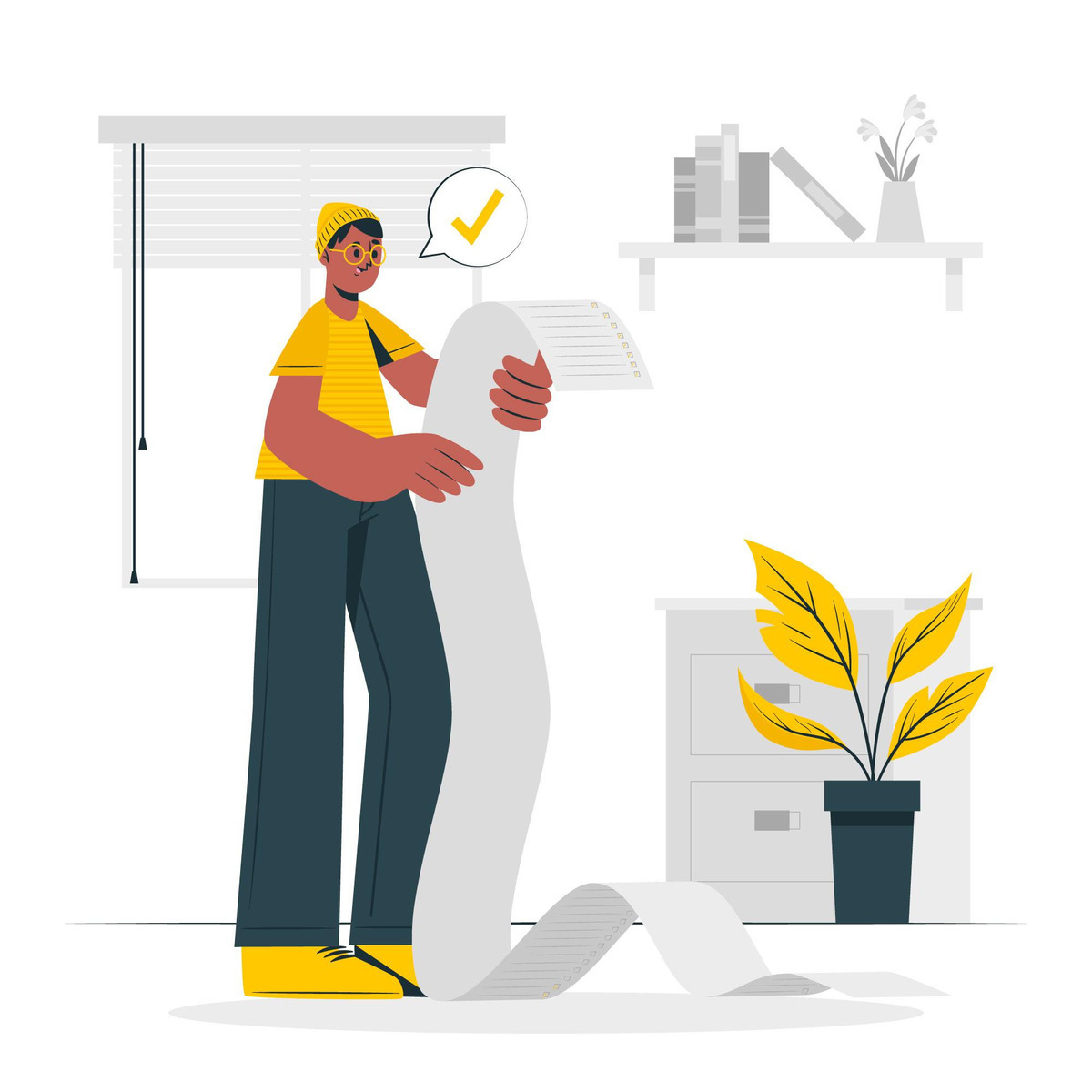
Stock-taking. A task that makes you lose your breath or get you exited?
Regardless of your starting point our four tips will make your stock-taking become succesfull.
Let’s jump right into it.
1: All or nothing
Stock-taking requires focus, so do it all at once. If you sell or use from the inventory during your stock-taking you’ll lose track of your counting.
If you’re only half done you cannot use your stock-taking and you’ll have to start all over again.
2: Promote stock-taking
To be in top of your stock-taking, we recommend the following:
- plan your stock-taking well in advance. Create as a recurring event in your joint calendar. Block all day and encourage everybody to abide by it
- Designate a project manager to prioritize the task
- let the manager remind the staff of the importance of the stock-taking on staff metings
- reward staff when the stock-taking is done
Curious about how tracezilla can help you manage your inventory?
3: Count it all
Your inventory consists of all your goods. So when counting your inventory, remember all your locations:
- goods you have in external storage or at another manufacturer
- goods that you have already packed for sales orders. Maybe they are somewhere else in the warehouse
- goods in process
4: Divide the counting into smaller parts
When counting your inventory it’s important to count every lot separately even though it is the same stock keeping unit but with three different dates of expiry.
You can try dividing them into three groups with different information like this:
- Traceability: Every lot needs a separate trace to ensure traceability. The trace can be a lot-number, batch number, production date, exipiration date or such.
- Supplier: note the supplier of the lot
- Location: where is the good located?
So. To sum up.
Our four advices to succesfull stock-taking are:
- Do it thoroughly. Count all or nothing.
- Prioritise stock-taking - book all day.
- Count it all. All goods - all stocks.
- Count each lot seperatly.
The inventory doesn’t match?
If you discover discrepancies, it’s time to investigate and find the cause.
A discrepancy in inventory is often due to human error. Those cases provides a good opportunity to improve workflows to minimize the risk of errors in the future.
Good inventory management does not come easily. It takes detailed planning and control of your workflows.
We hope you can use tips above, when you are preparing for stock-taking
It will make your stock-taking much easier.
Do you need better management of your inventory?
Look closer at tracezilla.
Receive our newsletter
